Avec les chercheurs du LIST, ArcelorMittal Luxembourg veut identifier les meilleures solutions pour valoriser les pertes de chaleur sur ses sites, et se dit prêt à investir dans de nouvelles technologies.
Sur le site ArcelorMittal de Belval, la chasse au gaspillage énergétique n’a rien de nouveau : depuis 2018, le sidérurgiste récupère, par exemple, la chaleur perdue au niveau de son four de réchauffage pour l’injecter dans le réseau Sudcal et couvrir ainsi 70 % des besoins des quartiers Belval, Sommet et Nonnewisen, soit environ 4 000 foyers. À la clé, une économie de 18 000 MWh et plus de 5 000 tonnes de CO2 par an.
Pour aller plus loin, dès 2019, le géant de l’acier a conclu un partenariat de cinq ans avec le LIST afin que ses ingénieurs en énergie travaillent, aux côtés des chercheurs de l’institut, sur des projets beaucoup plus innovants en matière de performance énergétique.
«Nous avons conscience que nos processus de fabrication nécessitent une grande quantité d’énergie – chacun de nos fours électriques a une puissance installée qui équivaut à celle de la Ville de Luxembourg – donc il est de notre responsabilité de contribuer à la réduction de la consommation et d’explorer toutes les possibilités de récupération de la chaleur», assure Pierre Jacobs, CEO d’ArcelorMittal Luxembourg Produits longs.
Alors que les groupes de travail ont progressé sur trois thématiques principales – répertorier la chaleur perdue sur les sites de Belval, Differdange et Rodange, valoriser les scories, et convertir la chaleur perdue en électricité – c’est cette dernière piste qui a été creusée à travers le projet nommé «Heat2Power».
Aux commandes, Alexandre Bertrand, chercheur au LIST et expert en efficacité énergétique, une spécialité qui suscite un vif intérêt ces derniers mois : «Le téléphone n’arrête pas de sonner», confie-t-il. Et pour cette collaboration avec ArcelorMittal, il a fallu être inventif : «Une fois les différentes sources de chaleur perdue identifiées sur les sites, la question centrale était de savoir quoi faire de cette chaleur», explique-t-il.
Face aux nombreuses options – chauffer des bâtiments, produire de l’électricité – comportant chacune ses propres contraintes en termes de coûts mais aussi d’émissions de CO2, déterminer lesquelles présentent réellement un intérêt pour l’industriel relève de la mission impossible : «D’où l’idée de créer un algorithme d’optimisation qui permette à ArcelorMittal de faire les meilleurs choix», poursuit l’expert, qui annonce que ce logiciel sera opérationnel d’ici six mois.
Pas seulement un intérêt écologique
Au sidérurgiste de lancer, dans les prochaines années, la mise en œuvre des technologies pointées comme les plus pertinentes par l’algorithme du LIST : «Nous souhaitons concrétiser ce projet. Dès le logiciel prêt, on examinera comment l’utiliser le plus efficacement dans nos processus», annonce Pierre Jacobs, qui a été étonné de découvrir toutes les solutions de valorisation possibles, notamment celle des scories. Et forcément, avec la crise énergétique, le CEO n’y voit pas qu’un intérêt écologique : «C’est aussi très intéressant économiquement, parce qu’avec la hausse des prix, mécaniquement, notre seuil de rentabilité descend», note-t-il, alors qu’un haut-fourneau vient justement d’être mis à l’arrêt ces derniers jours sur le site de Fos-sur-Mer.
Face à la montée des prix de l’énergie, ces innovations «made in Luxembourg» pourraient donc bien être dupliquées à l’avenir dans certains des 60 pays où opère le sidérurgiste, a souligné Roland Bastian, chef d’ArcelorMittal Luxembourg.
Le four de Belval bientôt remplacé
L’analyse des excédents de chaleur a été menée sur les sites de Belval, Differdange et Rodange, où 2 000 personnes travaillent sur six lignes de production comportant un four électrique et deux laminoirs à Belval, pour la production de palplanche et de poutrelles, un four électrique et un laminoir à Differdange pour la production de grandes poutrelles, et un laminoir à Rodange pour la production de rails pour trams et ponts roulants, ou encore de cornières. La capacité de production atteint 2,3 millions de tonnes d’acier par an dont 2,1 millions destinées à l’international. Le four de Belval, en marche depuis 1997, sera bientôt remplacé par un nouveau modèle moins énergivore. Un projet à hauteur de 100 millions d’euros, qui fait partie du protocole d’accord signé avec le gouvernement il y a quelques semaines, qui fait de la décarbonation une priorité. C’est d’ailleurs ce chantier qui sera approfondi en 2023 et 2024 par les groupes de travail communs avec le LIST.
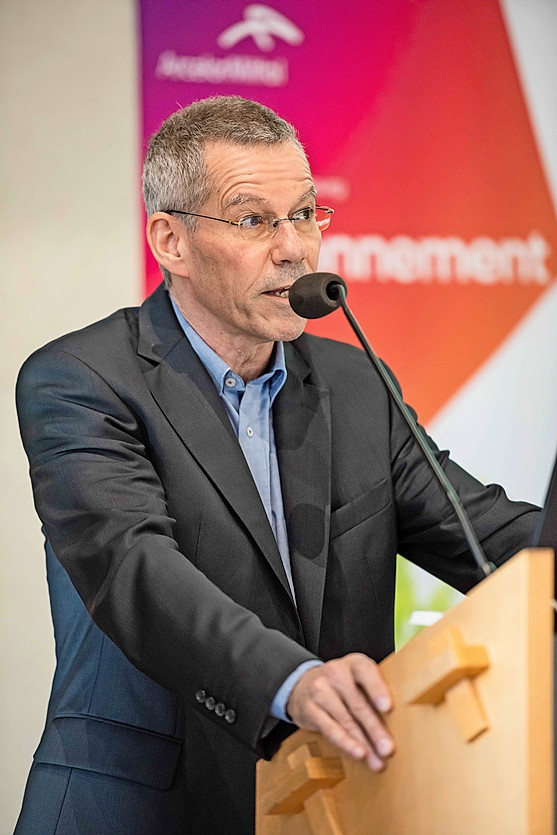